膠囊硫化罐的硫化效果與產(chǎn)品質(zhì)量密切相關(guān)。硫化效果的好壞直接影響硫化膠囊的性能和使用壽命,進(jìn)而影響到使用硫化膠囊生產(chǎn)的輪胎等橡膠制品的質(zhì)量。
硫化效果對(duì)產(chǎn)品質(zhì)量的影響
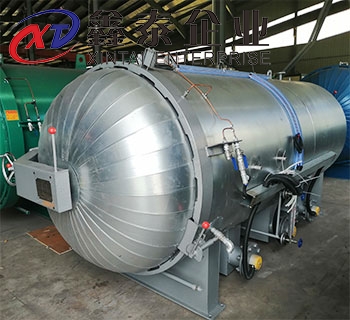
硫化程度的影響:
正硫化:硫化程度適中,膠料達(dá)到最佳的交聯(lián)狀態(tài),硫化膠囊的物理機(jī)械性能(如強(qiáng)度、耐撕裂性、耐熱性等)最佳。這樣的硫化膠囊在使用過(guò)程中不易損壞,能夠確保輪胎硫化質(zhì)量,提高輪胎的使用壽命和安全性。
欠硫:硫化程度不足,膠料交聯(lián)不完全,硫化膠囊的強(qiáng)度低、耐撕裂性差。使用欠硫的硫化膠囊進(jìn)行輪胎硫化,可能導(dǎo)致輪胎硫化不均勻,影響輪胎的性能和使用壽命。
過(guò)硫:硫化程度過(guò)高,膠料發(fā)生過(guò)度交聯(lián),硫化膠囊變硬、變脆,耐屈撓性能下降。過(guò)硫的硫化膠囊在使用過(guò)程中容易開裂,導(dǎo)致輪胎硫化失敗或質(zhì)量不穩(wěn)定。
硫化均勻性的影響:
硫化罐內(nèi)溫度和壓力的均勻性對(duì)硫化效果至關(guān)重要。如果硫化罐內(nèi)存在溫度或壓力梯度,會(huì)導(dǎo)致硫化膠囊不同部位的硫化程度不一致,出現(xiàn)局部欠硫或過(guò)硫的現(xiàn)象。這將嚴(yán)重影響硫化膠囊的性能和使用壽命,進(jìn)而影響輪胎等橡膠制品的質(zhì)量。
現(xiàn)代化的膠囊硫化罐采用先進(jìn)的自動(dòng)控制系統(tǒng),能夠精確控制硫化過(guò)程中的溫度、壓力和時(shí)間,確保硫化罐內(nèi)氣體和溫度的均勻分布,從而提高硫化膠囊的硫化均勻性和產(chǎn)品質(zhì)量。
硫化工藝參數(shù)的影響:
硫化溫度:硫化溫度是影響硫化速度和產(chǎn)品性能的關(guān)鍵因素。適當(dāng)?shù)牧蚧瘻囟瓤梢约涌炝蚧俣?,提高生產(chǎn)效率,同時(shí)保證硫化膠囊的性能。但是,過(guò)高的硫化溫度會(huì)導(dǎo)致橡膠分子鏈的裂解,降低硫化膠囊的性能。
硫化壓力:硫化壓力有助于排除膠料中的氣泡,提高膠料的致密性,使硫化膠囊與骨架材料緊密結(jié)合。適當(dāng)?shù)牧蚧瘔毫梢蕴岣吡蚧z囊的強(qiáng)度和耐屈撓性能。
硫化時(shí)間:硫化時(shí)間的長(zhǎng)短取決于硫化溫度和壓力。在適當(dāng)?shù)牧蚧瘻囟群蛪毫ο?,硫化時(shí)間應(yīng)足夠長(zhǎng),以確保膠料充分交聯(lián),達(dá)到最佳的硫化效果。
提高硫化效果和產(chǎn)品質(zhì)量的措施
選擇合適的硫化工藝參數(shù):
根據(jù)硫化膠囊的膠料配方和硫化體系,確定合適的硫化溫度、壓力和時(shí)間。
對(duì)于厚壁硫化膠囊或多部件硫化膠囊,應(yīng)采用逐步升溫或分段硫化的方法,以確保硫化均勻性。
優(yōu)化硫化罐的設(shè)計(jì)和操作:
采用先進(jìn)的自動(dòng)控制系統(tǒng),精確控制硫化過(guò)程中的溫度、壓力和時(shí)間。
定期對(duì)硫化罐進(jìn)行清洗和維護(hù),保持硫化罐內(nèi)部干凈,避免雜質(zhì)對(duì)硫化效果的影響。
合理設(shè)計(jì)硫化罐的容積和形狀,以適應(yīng)不同規(guī)格和數(shù)量的硫化膠囊硫化需求。
加強(qiáng)原材料和工藝過(guò)程控制:
嚴(yán)格控制原材料的質(zhì)量,確保膠料配方準(zhǔn)確,無(wú)雜質(zhì)混入。
對(duì)硫化工藝過(guò)程進(jìn)行實(shí)時(shí)監(jiān)控和調(diào)整,確保硫化效果穩(wěn)定可靠。
對(duì)硫化后的硫化膠囊進(jìn)行質(zhì)量檢測(cè),剔除不合格品,確保產(chǎn)品質(zhì)量。
結(jié)論
膠囊硫化罐的硫化效果與產(chǎn)品質(zhì)量密切相關(guān)。通過(guò)選擇合適的硫化工藝參數(shù)、優(yōu)化硫化罐的設(shè)計(jì)和操作、加強(qiáng)原材料和工藝過(guò)程控制等措施,可以提高硫化效果,確保硫化膠囊的性能和使用壽命,進(jìn)而提升使用硫化膠囊生產(chǎn)的輪胎等橡膠制品的質(zhì)量。